WELCOME TO OUR FOLK LIFT TRAINING CENTRE IN JOHANNESBURG AND BOTSWANA +27788735391
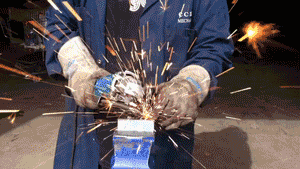
TLB, FORKLIFT, FRONT END LOADER, EXCAVATOR, MOBILE CRANE,TOWER CRANE, OVERHEAD CRANE, DUMP TRUCK, LOAD HAUL DUMPER LHD, ROAD ROLLER, SKID STEER (BOB CUT),RIGGING /RIGGER, REACH TRUCK, GRADER,BULL DOZER, FIRE FIGHTING,COMBINEDRIGID VEHICLE, TRUCK DRIVING, RIGID VEHICLE(BUS) DRILL RYK, O.H.S, FIRST AID, DANGEROUS GOODS (HAZKEM) TRACTOR LOADER BACKHOE,COUNTER BALANCE (FORKLIFT), CONTAINER FORKLIFT,AND MANY MORE. YOUR ALL WELCOMED TO OUR TRAINING CENTRE +27788735391 .
Friday, October 19, 2018
BOILERMAKER WELDING TRADE TEST EXCAVATOR, MOBILE CRANE,TOWER CRANE, OVERHEAD CRANE, DUMP TRUCK, LOAD HAUL DUMPER LHD FORKLIFT TRAINING CENTER +27788735391
TIG welding (Tungsten Inert Gas welding) is a type of welding that is ideally suited to tricky shapes like curves and corners. It offers precision, accuracy, and quality — and a great appearance when done correctly.
TIG welding is used in a wide variety of applications and industries. It is commonly used in the building of aircraft, ships, and other vehicles, particularly in pipework and sheet metal. The process can be carried out in tight spaces and so is often performed ‘in the field’ as well as in workshops. With such a visually pleasing appearance, TIG welding is also used in architectural work and art.
It’s not the easiest type of welding to master so it’s not the best place to start if you’re completely new to welding. If you have some experience under your belt though, TIG welding is well worth getting into. It’s versatile, highly skilled, and immensely rewarding.
Ready to get started with TIG welding?
How is TIG welding different?
So what makes TIG so difficult to learn?
There’s a lot to think about: there are tons of settings to choose from and you’ll probably need to use a foot pedal to control the current while holding the torch and feeding the filler rod. You’ll also have very little room for error with your arc length, and the tungsten electrode cannot touch the workpiece.
Phew! Let’s break it down.
TIG uses a non-consumable, pointed tungsten electrode to deliver the electric current. The pointed electrode creates a small, intense arc that allows for greater precision. It’s also more difficult to control, so it takes some practice to get used to — especially as the arc must be kept a specific length for the correct results. On top of that, the tungsten cannot touch the work surface, or else it will get contaminated and need grinding.
Many TIG welding machines allow the current to be controlled via a remote foot pedal. During the weld, the current can be increased or decreased with the pedal to create more or less heat, similar to the gas pedal in a car. This allows for a huge amount of control throughout the weld. In addition, there are many settings that can be adjusted on the TIG welding machine.
To put it simply, there’s a lot of coordination and dexterity involved.
Don’t be put off though! A filler material is optional, so you don’t need to worry about that, to begin with. And if you’re comfortable with other types of welding, TIG will be easier to pick up. It’s all about practice, practice, practice.
What you need to TIG weld
As well as practicing, you also need to get familiar and comfortable with the different settings on the TIG welding machine, and what they do. We won’t cover them all here, the main thing to think about is the current.
Power
A TIG welding machine can operate on an AC or DC current. For welding steels, a DC current should be used. For alloys, use AC.
The base current is set on the machine and remains constant. TIG welding machines allow you to build up to the base current, which is useful for preventing the thermal shock of the workpiece.
To achieve a soft start, a foot pedal can be used or a minimum current can be set on the machine. When the arc is started, the current will increase from the minimum to the base current, over a time period which can also be set. The same can be applied in reverse when the weld is complete.
Welding is a fabrication process that joins two or more metals using heat, pressure, or both to form a strong, permanent bond. Weldable materials generally include metals and thermoplastics, but welding other materials like wood are also possible.
Modern welding was pioneered in 1800 when Sir Humphry Davy struck an electric arc using a battery and two carbon electrodes. Since then, welding has developed into highly versatile forms, paving the way for its use in a variety of applications, from small DIY projects to large-scale manufacturing assemblies.
Different welding processes are a staple in most industry sectors and thus, let’s understand how these work and the principles behind them.
How Does Welding Work?
Welding is a high-heat process that melts the base materials. This is also the main differentiating factor from soldering and brazing where only the filler material is melted and no fusion between the parent materials occurs.
Welding works by joining two or more workpieces together at high temperatures. The heat causes a weld pool of molten material which after undergoing cooling, solidifies as one piece, forming a weld. The weld can even be stronger than the parent metals.
There are many different types of welding but all of them involve heat or pressure to melt the metals to create welded joints. The source of heat or pressure may vary depending on the application and the material used.
Metals are known as the most commonly welded materials, given their easy and straightforward welding principles. Plastic welding is also quite widespread but welding wood is just in its nascent phase.
The welding process is influenced by many factors, such as the need for specific additional tools, shielding gases, welding electrodes and filler material. Let’s have a closer look at some of the most common welding methods used today and find out what makes each of them unique.
Different Welding Types
Although the fundamental concept of welding is rather simple, we categorise them by the energy source used. As we break these subcategories down even further, we can dive deeper into the operating principles behind each separate method.
Arc Welding
Arc welding includes some of the most well-known welding processes and these are most likely what come to mind when visualising the welding process in general. In these processes, an electric arc generates heat between the electrode and the metal to be welded. The electrode may be consumable or non-consumable, and its power source can vary from alternating (AC) to direct current (DC).
MIG/MAG Welding
Gas metal arc welding (GMAW), also known as MIG/MAG welding (metal inert gas/metal active gas), uses a continuous wire electrode fed through a welding gun. As the electric arc melts the electrode wire it is then fused along with the base metals in the weld pool.
Shielding gas is simultaneously supplied to the weld area to create a protective layer from atmospheric contamination.
The simplicity of this welding technique allows it to be one of the preferred choices for industrial welding, manufacturing, construction and for the automotive sector. GMAW has pretty much replaced atomic hydrogen welding (AHW), mainly because of the availability of inexpensive inert gases.
TIG Welding
Tungsten inert gas welding uses a non-consumable tungsten electrode and an inert shielding gas. In contrast to MIG/MAG welding, using separate filler metal in TIG welds is optional and depends on the project.
The gas tungsten arc welding (GTAW) process creates accurate and high-quality welds with great penetration making it suitable for several applications, such as aerospace and automotive industries. While TIG welding has a steeper learning curve than MIG welding, the many adjustable features and functions of a TIG welder make it a very versatile process.
Shielded Metal Arc Welding
Shielded metal arc welding (SMAW) also known as manual metal arc welding (MMAW/MMA) or just stick welding, uses a consumable flux-coated metal electrode to join metals.
As we strike the electrode with the base metal, it creates an arc that melts down the materials in the weld pool. The flux releases a shielding gas to protect the weld metal from contamination. Slag deposits are removed after the cooling process using common shop tools such as a wire brush.
SMAW is a reliable welding process that offers versatility in welding different metals and various conditions. It’s also portable and lightweight, with no need for a gas tank as with some of the other welding methods mentioned previously. The welding electrode comes as a welding rod, making it perfect for tight spaces and awkward welding positions.
Flux-Cored Arc Welding
Fluc-cored arc welding process performed outdoors to weld steel structures
Flux-cored arc welding (FCAW) is an automatic or semiautomatic process that uses a welding electrode that contains a flux core that acts as a shielding agent. Additional protection from contaminants is called dual-shielded FCAW, wherein a shielding gas is used along with the flux-cored electrode.
FCAW is well-suited for ferrous metals and operations requiring little pre-cleaning. It is best used for repairs, pipes, shipbuilding, outdoor and underwater welding because of its incredible protection from external conditions.
Although FCAW and GMAW are two separate welding types, the only major difference lies in shielding the weld zone using electrodes and shielding gases.
CONTACT 0788735391
EMAIL bagvintraining82@gmail.com
Subscribe to:
Post Comments (Atom)
DRILL RIG AND ROCK DILL OPERATOR TRAINING 0788735391
Drill rig operator training courses South Africa Heavy machines training courses college. The school of heavy machinery training and we...

-
TIG welding (Tungsten Inert Gas welding) is a type of welding that is ideally suited to tricky shapes like curves and corners. It offers pre...
-
WELCOME TO OUR FOLK LIFT TRAINING CENTRE IN JOHANNESBURG AND BOTSWANA +27788735391 www.bagvinforklifttraining.blogspot.com WE OFFER ...
-
Forklift driving training in Boksburg,Rigging , Operation of a Reach stacker ,Bobcat Skid Steer Loaders ,Tractor Loader Backhoe TLB , accr...
No comments:
Post a Comment